- Trang chủ|Tư Vấn Giải Pháp Xử Lý Chất Thải Rắn
Tư Vấn Giải Pháp Xử Lý Chất Thải Rắn
The word pyrolysis comes from Greek, where pyro means ‘fire’ and lysis means ‘to separate’. The pyrolysis process is based on different methods of thermal decomposition at various degrees that can vary from 300°C to 900°C. Pyrolysis-derived plastics can be complex and are often difficult to reuse for further refining. This is because many pyrolysis systems use very high temperatures, which reduces the quality of the final product. In order to achieve a high-quality final product, pyrolysis chamber temperature is a critical factor.
Pyrolysis technology — turning plastic to petrochemical products — has enormous potential for plastics in general. This is especially true for mixed plastics, which accounts for up to 80 % of all plastic waste, and is currently mostly being incinerated.
As of yet, there are no pyrolysis facilities in operation in Norway.
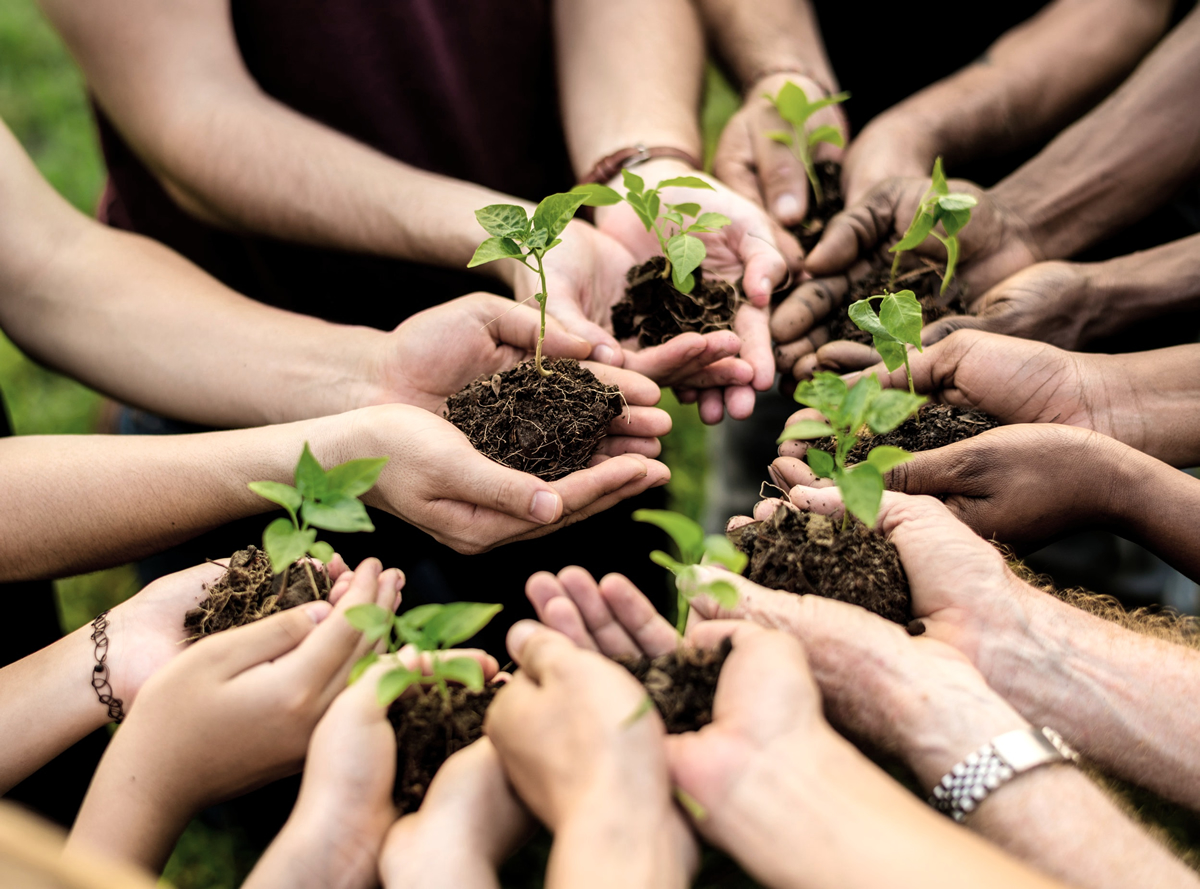
Halden Plastic Recycling and the Municipality of Halden want to be first mover in order to become an important driving force in the implementation of new technology.
7920 tons of waste plastics in one year from Halden plant at Rokke Waste Facility to petrochemical products, will in addition reduce approximately 15444 tonnes of CO2 equivalents emissions into the atmosphere.
OUR TECHNOLOGY
Our proven pyrolysis technology uses low temperatures and does not require a catalyst. In this process, the plastic is transformed into oil, gas and carbon black through a chemical and physical separation process.
This technology is efficient and yields a utilization rate of 60–90 %, depending on the quality of the plastic input.
These end products can be further processed into environmentally friendly fuels, new plastics or a variety of petrochemical end products.
The pyrolysis process is more robust against mixed plastics, which are otherwise typically incinerated, put in landfills or released into the environment.
Our technology partner